PROJECT STORY
「この国で、あの国で。YACの生産秘話」篇
2018年02月-
製造開発担当:M・O
商品開発部/1998年入社
製造開発リーダー -
購買担当:T・S
商品部/2008年入社
購買担当
ギョーカイ初挑戦!「車種専用商品」開発物語<3>
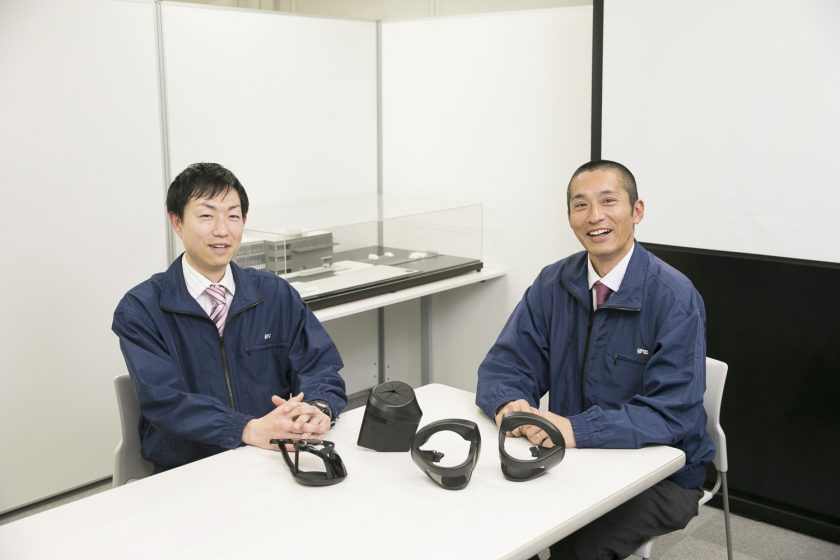
自社生産設備を持たない槌屋ヤックなので商品のほとんどが海外生産だから、それをきちんとした品質で量産していく体制を作るのはホネが折れますよね。
そうだね。まずは納期やコストが決められて、最後は僕たち製造開発の役目だからね。設計サイドとしてはできるだけ組み立てを簡素化させたりしているけど、それがその通りにいかないことも。
設計では寸分違わず誤差ゼロで考えるわけですが、それじゃあ量産する時に問題になる場合もあるってことですよね。どこまでクリアランスが必要なのか、意匠デザイン的にはどこまでが許容範囲なのか、検討しながら品質を保っていくのも面白さ(?)ですかね。
海外の協力会社によっても違うからねえ。A社ならこのままの図面でいけるけど、B社に委託する場合は設計図をこう描いたほうがいいかなとか考えるよ。得意不得意があるし。この程度の誤差ならいいんじゃない!って判断されることもあるけど、より良いものをつくるために妥協はできないから。そんな時は厳しく指示しないといけないことだってある。こんな穏やかなボクなのに…。
見えにくいところだから大丈夫だろうとか、手直ししていたら間に合わないとか、ウチの商品が保つべき品質に近づけていくまでには現地でたいへんな苦労しているわけですねえ。そういう時のネゴシエーション術はどうやって学ぶのですか?
最初はとにかく先輩についてまわって、その現場を間近で見て覚えたかな。“ボクの頼みだからヨロシクね”って言えるような良好な関係をつくる。それができないところもあるけどね。中国語は完全に理解していないけど、出来る限り中国語で話しかけることで、だんだん距離が近くなって、少しずつ信頼関係が築けていくんだよ。
へえ。ボクは日本での購買が主体なので違うことを考えます。たとえば不具合を先に予見できるかですね。これは思ったより製品の色落ちが進みやすいんじゃないのか?とか他社商品ではこんな不具合が起きているようだけれど、ウチの製品でもその問題が発生する可能性があるのか?なんて。先回りして考えることが大切ですね。ロングセラー商品なんかは金型自体が経年劣化で不具合も発生しやすくなったりしますからね。ロットが少なくても安定供給するためにはどうしたら最適なんだろうか…なんて考えることは山積みです。
もうホントにいろんなところに視点を注がなきゃいけないからねえ。納期に貿易に生産管理に‥‥。近ごろは年間で100日以上海外に出張しているんだけれど、急に髪が真っ白になってきてさ。これは経年劣化じゃないと思いたいんだけどね。
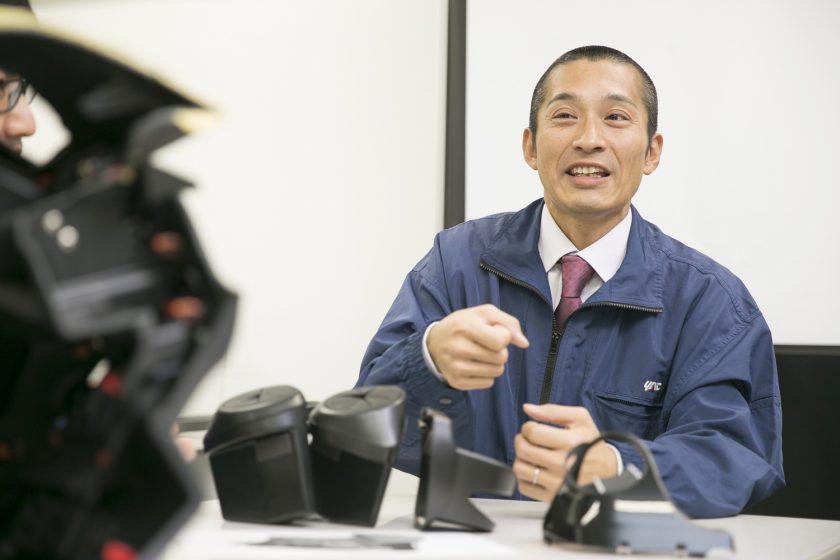
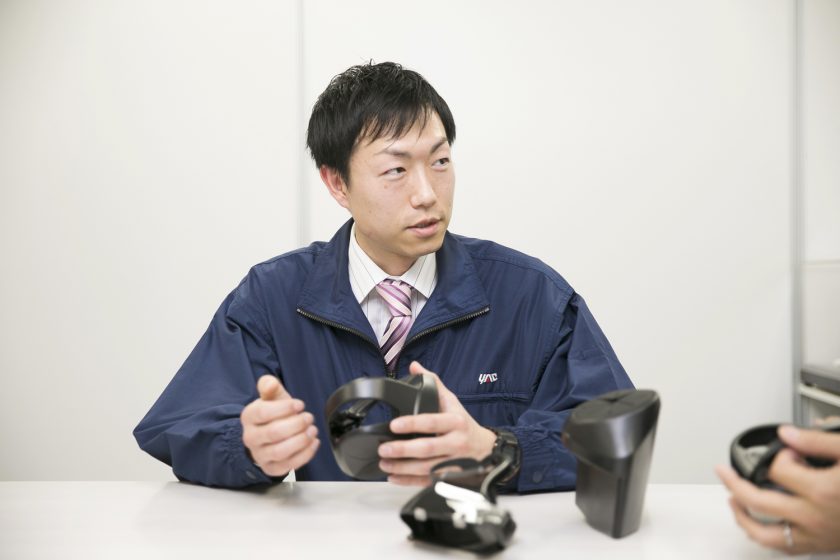
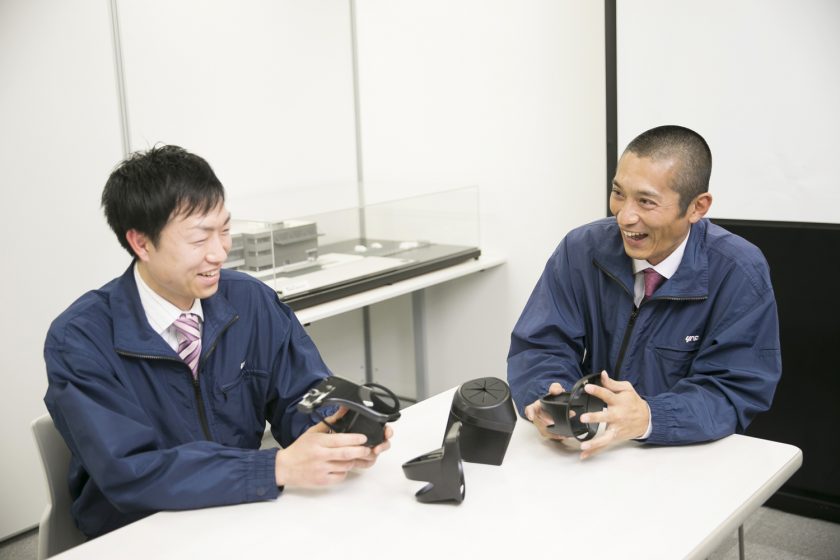